Jika Anda adalah seorang operator gudang atau pemilik bisnis yang operasi bisnisnya berhubungan dengan banyak SKU dan pergudangang, penting bagi Anda untuk menhetahui apa itu batch picking.
Operasi gudang terus berupaya untuk mengurangi biaya operasional dan meningkatkan hasil produksi. Langkah yang tidak dapat diabaikan untuk mencapai tujuan tersebut adalah proses pengambilan, karena semakin lama waktu yang dibutuhkan untuk memenuhi pesanan, semakin tidak menguntungkan pesanan tersebut.
Batch picking adalah metodologi pengambilan pesanan yang, jika diterapkan dengan benar, dapat meningkatkan efisiensi pengambilan dengan mengelompokkan beberapa pesanan serupa ke dalam satu instruksi pengambilan.
Pada artikel kali ini, kami akan membahas apa itu batch picking, cara kerja, manfaat, sampai contoh kasusnya yang akan memudahkan Anda untuk mengerti konsep ini.
Apa yang Dimaksud dengan Batch Picking?
Batch picking, juga disebut batching atau multi-pesanan, adalah metode pengambilan pesanan di mana petugas secara bersamaan mengumpulkan barang untuk beberapa pesanan.
Batch picking umumnya lebih cepat daripada strategi pengambilan lainnya – seperti pengambilan pesanan tunggal, di mana petugas mengambil satu pesanan dalam satu waktu – karena mengurangi waktu perjalanan ke gudang.
Para petugas melaporkan bahwa mereka harus berjalan sejauh 16 km per hari untuk melakukan pekerjaan mereka, tetapi batch picking menghilangkan kebutuhan untuk berulang kali mengunjungi lokasi pengambilan yang sama beberapa kali dalam satu shift saat mereka memenuhi pesanan, sehingga mengurangi waktu perjalanan secara signifikan.
Batch biasanya terdiri dari sekitar delapan hingga 20 pesanan serupa yang dikonsolidasikan ke dalam satu daftar pengambilan.
Pesanan yang digabungkan secara bersamaan umumnya memiliki beberapa item yang sama atau bahkan jalur pengambilan yang sangat mirip.
Untuk menetapkan pengelompokan batch dan rute pengambilan yang optimal, penting untuk menggunakan sistem manajemen gudang atau warehouse management system (WMS) dan sistem manajemen pesanan atau order management system (OMS).
WMS dan OMS dapat menganalisis pesanan dan tata letak gudang spesifik Anda untuk membuat rencana pengambilan yang meminimalkan waktu perjalanan, sehingga menghasilkan lebih banyak waktu yang dihabiskan untuk mengambil dan lebih sedikit waktu yang dihabiskan untuk berjalan.
Batch picking dapat menjadi sangat produktif karena pekerja dapat mengambil banyak SKU untuk beberapa pesanan dalam satu perjalanan, daripada melakukan perjalanan yang terpisah dan berulang-ulang di seluruh gudang.
Selain itu, dengan melakukan batch picking berarti lebih sedikit orang yang bergerak melalui lorong gudang pada satu waktu.
Hal ini menyebabkan lebih sedikit hambatan, sehingga pekerja dapat mencapai tujuan mereka dengan lebih cepat. Pesanan kemudian harus disortir di area pengemasan ke dalam kotak yang sesuai.
Perbedaan batch dan wave picking
Dalam batch picking, satu petugas mengambil sejumlah pesanan pada waktu yang sama.
Tujuannya adalah untuk menciptakan jalur pengambilan yang optimal yang mencegah petugas mengambil barang yang sama beberapa kali saat memenuhi banyak pesanan.
Dalam wave picking, manajer gudang menjadwalkan waktu pengambilan – atau gelombang – sepanjang hari. Tujuannya, pesanan dikirim untuk dipenuhi berdasarkan apa yang ada di dalamnya sehingga pesanan yang serupa dapat dipenuhi bersama; ini seperti selangkah lebih maju dari batch picking.
Baca juga: 17 Cara Melakukan Analisis Prediktif dalam Bisnis Retail
Perbedaan batch dan zone picking
Zone picking adalah cara populer lainnya untuk meningkatkan efisiensi pengambilan pesanan.
Dalam batch picking, satu petugas biasanya akan memenuhi beberapa pesanan secara penuh. Dalam zone picking, satu pesanan dibagi di antara beberapa petugas yang mengambil barang yang berbeda dalam pesanan yang berada di area (atau zona) yang sama di gudang.
Setiap petugas pengambilan diberi zona di gudang dan hanya mengambil SKU dari zona tersebut.
Setelah petugas mengambil SKU yang diperlukan dari batch mereka, mereka dapat memasukkannya ke dalam tas jinjing dan meneruskannya ke zona berikutnya sampai seluruh pesanan diambil.
Seperti batch picking, zone picking dapat meningkatkan efisiensi pengambilan dengan mengurangi waktu perjalanan.
Namun, zone picking tidak mengharuskan pesanan dikelompokkan bersama. Hal ini membuat zone picking menjadi pilihan yang lebih baik untuk bisnis yang tidak secara teratur menangani pesanan serupa.
Namun, tergantung pada kebutuhan pengambilan di gudang, zone picking dapat dikombinasikan dengan strategi pengambilan lainnya, seperti wave picking, batch picking, atau keduanya.
Bagaimana Cara Kerja Batch Picking?
Dengan adanya WMS atau OMS untuk menentukan batch yang optimal dan memetakan rute pengambilan, batch picking adalah proses yang cukup mudah. Berikut cara kerjanya:
Buat daftar pengambilan
WMS atau OMS biasanya menghasilkan daftar konsolidasi dengan SKU, jumlah, dan lokasi penyimpanan inventaris.
Daftar pengambilan dapat dibuat secara manual, tetapi WMS atau OMS dapat secara otomatis mengumpulkan pesanan serupa – seperti pesanan yang terdiri dari banyak SKU yang sama atau memerlukan jalur pengambilan yang serupa – untuk menyederhanakan operasi pengambilan dan mengurangi waktu perjalanan.
Tetapkan dan persiapkan petugas pengambilan
Petugas menerima daftar pengambilan dan mengumpulkan peralatan yang diperlukan untuk menyelesaikan setiap pesanan, seperti tas jinjing, troli, dan pemindai seluler.
Beberapa operasi mungkin menggunakan teknologi tambahan seperti headset pengambilan suara, yang mengarahkan petugas pengambilan ke lokasi setiap item yang termasuk dalam pesanan.
Baca juga: Metode Analisis Persediaan atau Inventory Analysis, KPI, dan Tipsnya
Ambil barang
Ada beberapa cara untuk mengambil barang, biasanya tergantung pada kebutuhan bisnis.
Beberapa gudang mungkin memiliki petugas yang mendorong troli yang menampung beberapa jinjingan kecil untuk setiap pesanan, sementara yang lain mungkin memiliki pekerja yang mengambil langsung ke dalam kotak pengiriman.
Yang lain mungkin mengumpulkan semua SKU serupa ke dalam satu palet yang kemudian dikirim ke tim pengepakan untuk disortir dan disiapkan untuk pengiriman.
Apa pun metodenya, para pekerja memilih mengikuti daftar pengambilan sesuai dengan jalur yang telah ditentukan, dengan fokus pada satu SKU dalam satu waktu.
Pekerja sering kali menggunakan pemindai barcode seluler untuk melacak kapan mereka mengambil setiap item dan jumlah yang dibutuhkan.
Kemas dan kirim pesanan
Jika pesanan tidak disortir dan dikemas ke dalam wadah selama proses pengambilan, barang yang diambil akan dikirim ke penyortir yang akan memisahkan barang ke dalam pesanan masing-masing.
Pesanan kemudian dikemas dengan tepat dan disiapkan untuk pengiriman. Sementara itu, petugas mulai mengambil pesanan berikutnya.
Baca juga: Biaya Persediaan (Inventory Costing): Pengertian, Metode dan Contohnya
Manfaat Batch Picking
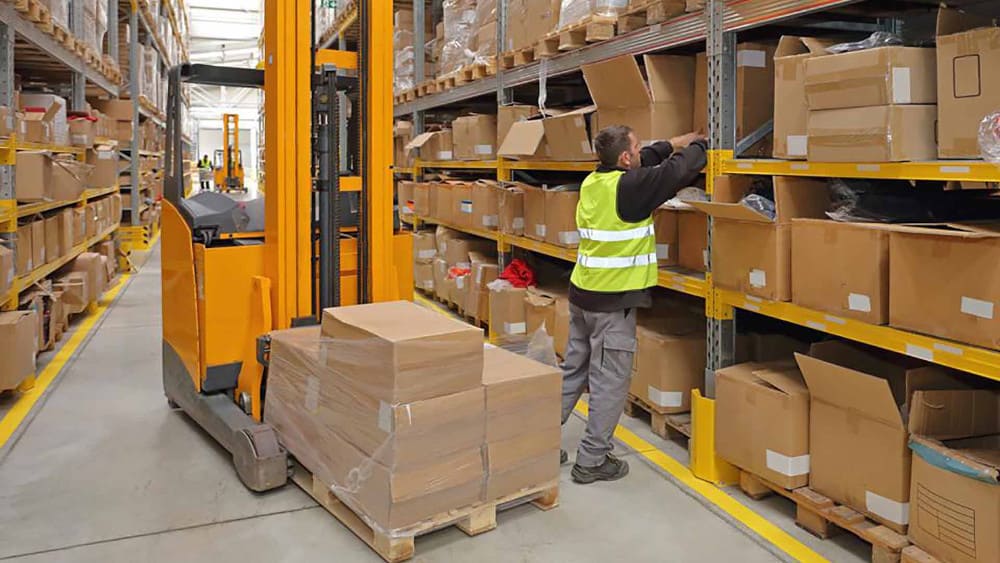
Pengambilan yang cepat dan akurat tidak hanya penting untuk menyederhanakan operasi pemenuhan pesanan, tetapi juga untuk kesuksesan jangka panjang bisnis.
Ketika pelanggan menerima pesanan yang akurat dengan cepat, mereka cenderung puas dan menjadi pembeli yang loyal.
Banyak operasi gudang yang dapat memperoleh manfaat dari batch picking karena:
Lebih efisien
Dibandingkan dengan strategi pengambilan pesanan lainnya, seperti pengambilan pesanan tunggal, batch picking lebih efisien karena pekerja dapat mengambil barang untuk beberapa pesanan sekaligus, alih-alih mengunjungi lokasi penyimpanan yang sama beberapa kali dalam satu shift.
Hal ini memungkinkan tingkat pengambilan yang lebih cepat
Selain dapat mengambil beberapa item sekaligus, batch picking membantu mencegah pengambilan secara sporadis.
Hal ini umumnya berarti lebih sedikit banyak petugas yang menavigasi lorong gudang pada saat tertentu, mengurangi hambatan dan membantu staf mencapai lokasi pengambilan berikutnya dengan lebih cepat.
Ini mengurangi waktu perjalanan
Dengan rute pengambilan yang ditentukan yang bertujuan untuk memaksimalkan setiap langkah yang diambil, petugas gudang dapat menghindari mundur atau mengulangi jalur pengambilan yang sama beberapa kali dalam shift tertentu.
Hal ini dapat sangat mengurangi waktu perjalanan, sehingga meningkatkan efisiensi pengambilan.
Mengurangi stres pada tenaga kerja
batch picking dapat mengurangi waktu yang dihabiskan untuk melintasi gudang, sehingga pekerjaan ini tidak terlalu membebani pekerja secara fisik.
Dan karena petugas pengambilan tetap fokus pada satu SKU dalam satu waktu, akan lebih mudah untuk fokus pada apa yang ada di depan mereka, meminimalkan kelelahan mental dan meningkatkan akurasi.
Baca juga: Sistem Persediaan Periodik: Pengertian, Contoh, Manfaat, dan Tantangannya
Contoh Batch Picking
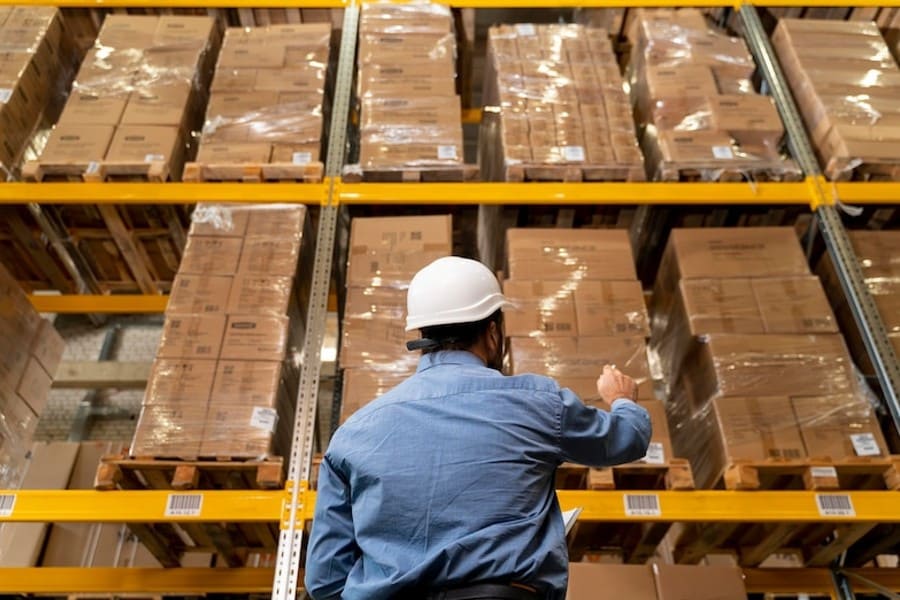
Untuk lebih memahami proses batch picking, akan sangat membantu jika kita melihat sebuah contoh. Bayangkan ada tiga pesanan pelanggan yang perlu diambil:
Pelanggan A
- 40 paket baterai AAA
- 20 unit lampu LED kawat tembaga
- 12 mesin pemotong rumput
Pelanggan B
- 20 paket baterai AAA
- 10 mesin pemotong rumput
- 5 sekop tangan
Pelanggan C
- 10 paket baterai AAA
- 5 unit lampu LED kawat tembaga
Daripada mengambil setiap pesanan pelanggan satu per satu sebelum melanjutkan ke pesanan berikutnya, pekerja gudang yang menggunakan pengambilan secara berkelompok dapat mengambil semua 70 paket baterai AAA untuk semua pelanggan terlebih dahulu dan menempatkannya di dalam tas yang telah ditentukan di troli.
Selanjutnya, petugas mengambil semua 25 unit lampu LED kabel tembaga dan menempatkannya di tas lain di gerobak yang sama. Kemudian petugas mengambil lima sekop tangan untuk pelanggan B dan menempatkannya di troli lain.
Sebelum mengambil mesin pemotong rumput untuk pelanggan A dan B – yang berukuran besar dan tidak muat di troli – petugas gudang membawa semua baterai, lampu LED, dan sekop ke area pemilahan.
Terakhir, petugas gudang menggunakan dongkrak palet untuk mengumpulkan semua 22 mesin pemotong rumput di satu palet dan membawanya ke area pemilahan untuk disortir dan dikemas untuk dikirim bersama barang lainnya.
Baca juga: Mengenal Apa Itu Sistem Persediaan Perpetual untuk Pemilik Bisnis
Studi Kasus Batch Picking
Batch picking dapat memangkas biaya secara signifikan jika diterapkan dengan benar.
Sebagai contoh, sebuah apotek keluarga dengan gudang pusat yang mendistribusikan barang ke 50 toko ritelnya di jabodetabek.
Setelah perusahaan membuka 15 lokasi baru, pusat distribusinya berjuang untuk memenuhi permintaan.
Mengingat skala perusahaan yang cukup kecil, perusahaan memilih untuk menilai kembali strategi pengambilan pesanannya sebelum memasukkan proses otomatis lainnya.
Setelah melakukan analisis, manajer gudang menyadari bahwa pengambilan pesanan tunggal tidak lagi cocok digunakan, terutama karena setiap lokasi ritel umumnya memesan jenis barang yang sama, sehingga mereka beralih ke batch picking.
Untuk setiap shift, manajer menggunakan WMS mereka untuk menetapkan batch pesanan yang optimal dan rute pengambilan yang memungkinkan pekerja mengambil beberapa pesanan sekaligus, alih-alih berulang kali melakukan perjalanan yang sama di seluruh gudang.
Pada akhirnya, apotek tersebut dapat memangkas waktu perjalanan pekerja sebesar 55% dan meningkatkan tingkat pengambilan sebesar 40%. Dan, meskipun terjadi peningkatan permintaan, peningkatan produktivitas memungkinkan perusahaan untuk mengurangi biaya tenaga kerja sebesar 15%.
Baca juga: Inventory Plan (Recana Persediaan): Proses dan Analisanya
Batch Picking dan Automasi
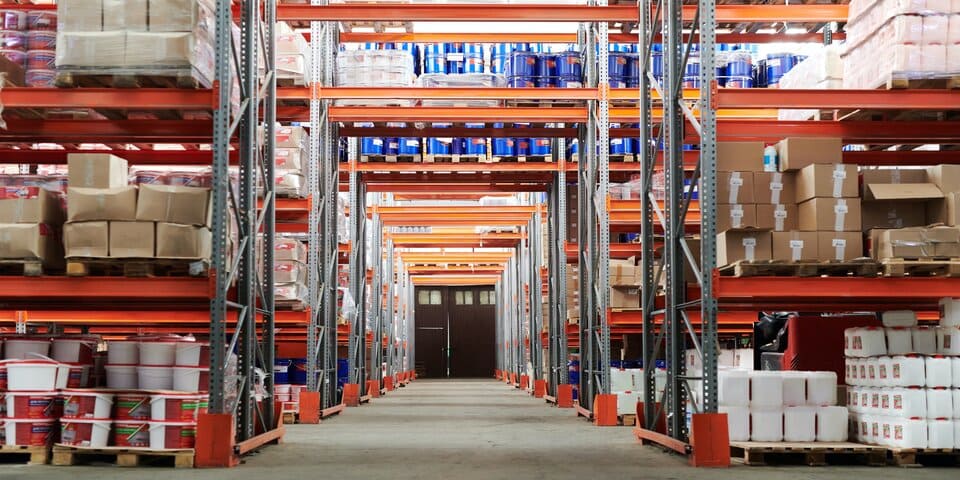
Meskipun batch picking dapat meningkatkan akurasi dan kecepatan dengan sendirinya, sistem otomatis yang menggunakan modul robotik atau semi-robotik dapat meningkatkan kemampuan pengambilan dan lebih mengoptimalkan proses pengambilan.
Berikut adalah beberapa jenis sistem otomatisasi gudang yang dapat diterapkan pada batch picking:
Robot
Seperti robot kolaboratif (“cobot”) dan robot seluler otonom atau autonomous mobile robots (AMR), meningkatkan proses pengambilan manual dengan bekerja secara kolaboratif dengan karyawan.
Cobot umumnya membantu petugas pengambilan dengan membantu mereka menavigasi ke lokasi pengambilan berikutnya dan memberikan informasi pengambilan penting lainnya, seperti jumlah SKU.
Atau, mereka mungkin membawa tempat sampah atau tas untuk petugas. AMR dapat menavigasi gudang secara mandiri dan menangani tugas-tugas seperti menyortir atau mengangkut inventaris dari titik A ke titik B.
Automated storage and retrieval systems (AS/RS)
Sistem ini dapat secara otomatis mengambil barang sesuai permintaan. Meskipun ada berbagai sistem AS/RS yang tersedia, vertical lift modules (VLM) sangat berguna untuk batch picking.
Unit penyimpanan ini pada dasarnya berfungsi seperti mesin penjual otomatis skala industri; baki rak dipasang di dalam lift pengambilan yang terletak di pusat.
Diarahkan oleh perangkat lunak, pengguna dapat memasukkan item yang perlu mereka akses, dan VLM mengirimkan rak masing-masing ke operator di titik akses.
Automated batch picking carts
Automated batch picking carts menggunakan software untuk mengoptimalkan rute pengambilan berdasarkan lokasi fisik troli secara real-time.
Troli itu sendiri memiliki komputer dan antarmuka visual sehingga petugas dapat merujuk daftar pilihan mereka, dan troli biasanya dapat menampung beberapa SKU atau barang terpisah.
Automated batch picking carts dapat meningkatkan efisiensi dengan menemukan pesanan pengambilan tunggal terdekat yang dapat dengan mudah diambil selama batch picking multi-pesanan yang ditugaskan.
Baca juga: Siklus Persediaan dan Pergudangan: Pengertian dan Cara Auditnya
Optimalkan Batch Picking Dengan Teknologi
Seperti yang telah disebutkan sebelumnya, manfaat batch picking dapat ditingkatkan lebih lanjut dengan menggunakan OMS, WMS, dan alat manajemen persediaan.
Misalnya, sistem manajemen pesanan dapat secara otomatis mengelola siklus hidup pesanan, mulai dari saat pesanan dilakukan hingga waktu pengiriman.
OMS dapat mengambil data pesanan tersebut untuk mengotomatiskan pemrosesan pesanan, sehingga menghilangkan proses manual yang dapat menyebabkan hambatan dan menyebabkan kesalahan manusia, sehingga lebih mudah untuk memenuhi pesanan dengan cepat dan akurat.
Sementara itu, sistem manajemen gudang dapat secara otomatis mengelola semua sumber daya di dalam pusat distribusi. WMS dapat membantu perusahaan melacak pengaturan gudang, lokasi tempat penyimpanan, dan inventaris.
Sistem ini juga dapat membantu mencegah kelebihan stok dan kehabisan stok serta terhubung dengan teknologi gudang seperti pemindai barcode, sehingga petugas dapat dengan mudah mengonfirmasi ketika mereka telah mengambil pesanan.
Selain itu, WMS dapat menggunakan data untuk mengelola tugas-tugas gudang dengan lebih baik, seperti membuat strategi pengambilan yang optimal berdasarkan jenis pesanan dan tata letak gudang.
Lalu, software manajemen inventaris juga dapat meningkatkan efisiensi pengambilan pesanan karena menyediakan gambaran umum inventaris secara real-time.
Hal ini dapat sangat berguna di gudang dengan produk yang bergerak cepat dan sering kali memerlukan re-stock atau pengisian ulan.
Setiap waktu yang dihabiskan untuk menunggu SKU diisi ulang adalah waktu yang terbuang dan pesanan yang membutuhkan waktu lebih lama untuk dikirim.
Alat manajemen persediaan dapat melacak produk apa yang perlu diisi ulang dan kapan, sehingga petugas tidak perlu menunggu untuk memenuhi pesanan.
Dengan memungkinkan petugas pengambilan barang untuk mengambil beberapa barang untuk beberapa pesanan pada saat yang sama, pengambilan barang secara batch merupakan salah satu cara bagi gudang dan pusat distribusi untuk memenuhi pesanan secara efisien.
Dikombinasikan dengan otomatisasi dan perangkat lunak seperti WMS atau OMS, proses pengambilan pesanan dapat dioptimalkan lebih lanjut dan membantu bisnis mengirimkan pesanan ke pelanggan dengan lebih cepat dan akurat.
- Ingin Melakukan Stock Opname? Perhatikan 8 Prosedur Ini - 9 Juli 2025
- Spend Culture dalam Bisnis: Pengertian dan Cara Optimasinya - 8 Juli 2025
- 6 Aplikasi Stok Barang Terbaik untuk Bisnis Tahun 2025, Praktis! - 30 Juni 2025